

EMBEDDED SYSTEMS AND FPGA SPECIALISTS
Engineering Consultation and Design
Complex systems don't have to come with complex engineering projects. Our embedded systems and FPGA expertise enables us to help our clients simplify and navigate the
engineering life cycle – from requirement and interface capture, to electronic design, FPGA design and
embedded software implementation.
Professional Training
We can customize a training program for your engineering team, small or large groups. We've delivered hundreds of hours' worth of professional training, both virtually and in-person, specializing in high-reliability and mission-critical design. Our content is tested and tailored to your organization's requirements.
Content Creation
Create tutorials, whitepapers, webinars, workshops, use cases and more to attract and convert your target audiences. Our founder, Adam Taylor, has spent years creating content that speaks to technical audiences of all skill levels. We'll work with you to find the best content strategy for your goals.
Experience Across Markets
From satellite systems in space, to predictive maintenance in the factory, to ADAS on the road, Adiuvo has experience helping our clients design systems that are reliable and meet the most stringent standards.
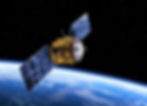


Building Trust and Better Systems
Helping our clients build better systems that they can deploy with confidence is always our number one priority. We treat our clients' challenges and goals as our own whether it be throughput, real-time performance, SWaP-C optimization, or yielding the maximum payload.
Taking on engineering projects in-house can be very challenging and quickly introduce problems like scope creep. Let us be your trusted partner and advisor. We bring not only proven experience to the table, but also an eye for building efficient systems that don't compromise.
.png)
Contact Us
Want to learn more about our services?
Send us a short summary of what you are interested in and we'll set up a free initial consultation to discuss your requirements.
Want to work with us?
Our client projects often require us to bring in expertise from different fields. Tell us a little bit more about yourself and let's connect!