top of page

Our aim is to create better FPGA engineering…
and better FPGA engineers.
Adiuvo designs FPGA systems for the some of the biggest names in the aerospace sector, as well as delivering consultancy, training and marketing services to leading chip manufacturers and other clients.
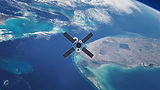


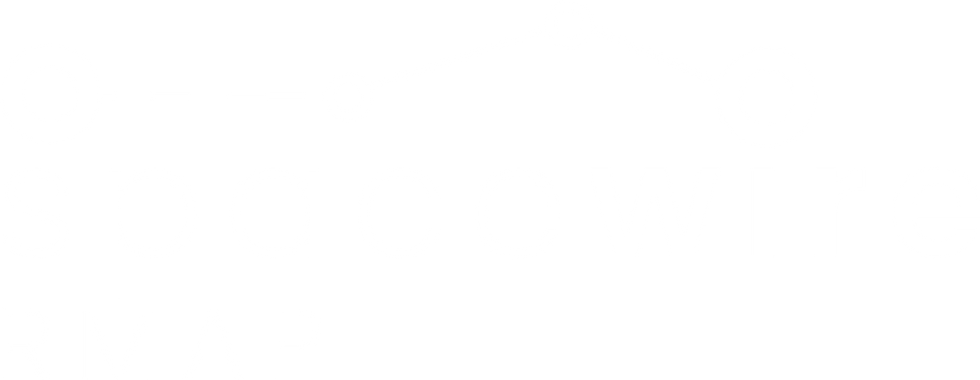
...for use across a range of FPGAs targeting space applications.

…for advanced prototyping or designing into missions
Featured Products
bottom of page